INNOVATIVE SPACE CARRIER INC.(CHUO-KU, TOKYO; CEO; KOJIRO HATADA, HEREAFTER REFERRED TO AS "ISC") IS "A WORLD WHERE PEOPLE AND CARGO ARE DELIVERED EVERY DAY. WE ARE A START-UP COMPANY THAT AIMS TO REALIZE A TRANSPORTATION SYSTEM THAT MAKES SPACE POSSIBLE. ( REUSABLE) IS A START-UP COMPANY THAT AIMS TO REALIZE A TRANSPORTATION SYSTEM THAT MAKES SPACE POSSIBLE.
WE ARE PLEASED TO ANNOUNCE THAT, IN COLLABORATION WITH WAAM3D, A UK-BASED 3D PRINTER MANUFACTURER WITH WHICH ISC HAS A PARTNERSHIP, CRANFIELD UNIVERSITY, AND AICHI SANGYO, A METAL 3D PRINTED PROPELLANT TANK HAS BEEN MANUFACTURED AND TESTED FOR PRESSURE RESISTANCE AND AIRTIGHTNESS WITHIN ONE YEAR FROM THE START OF THE STUDY.
THIS IS THE LARGEST TANK MANUFACTURED BY A METAL 3D PRINTER IN JAPAN.
AGILE DEVELOPMENT USING METAL 3D PRINTERS
FOUNDED IN MAY 2022, ISC HAS SET A CHALLENGING GOAL: "WE AIM TO PUT A SATELLITE INTO ORBIT BY 2028. TO ACHIEVE THIS GOAL, WE ARE PROMOTING AGILE DEVELOPMENT UTILIZING METAL 3D PRINTER TECHNOLOGY AS A MEANS TO DRAMATICALLY IMPROVE DEVELOPMENT EFFICIENCY.
AS PART OF THIS EFFORT, WE HAVE INTRODUCED WAAM* EQUIPMENT. CONVENTIONAL DEVELOPMENT METHODS REQUIRE LONG LEAD TIMES TO SECURE LARGE BLOCK MATERIALS AND PREPARE SPECIALIZED PROCESSING MACHINES, BUT THE USE OF WAAM TECHNOLOGY FACILITATES MATERIAL PROCUREMENT AND ENABLES DIRECT MOLDING OF THE REQUIRED SHAPES, MAKING DEVELOPMENT POSSIBLE IN A SHORT PERIOD OF TIME.
IN ADDITION, DEVELOPMENT WITH METAL 3D PRINTERS IS FLEXIBLE IN RESPONDING TO DESIGN CHANGES, AND REVISIONS CAN BE REFLECTED IMMEDIATELY AND NEW MODELING CAN BE PERFORMED QUICKLY. THIS FEATURE IS EXPECTED TO SHORTEN DEVELOPMENT CYCLES AND INCREASE DESIGN FLEXIBILITY.
* WAAM: Wire Arc Additive Manufacturing, a method of welding and laminating metal wires by melting them using the heat of arc discharge.
MANUFACTURE OF PROPELLANT TANK BY METAL 3D PRINTER. DEMONSTRATED WITHIN ONE YEAR OF STARTING DEVELOPMENT.
ISC has been developing product requirements and studying the design and manufacturing process for the development of a Flight Model (FM) propellant tank since April, following the production of a rear structural mockup of the rocket in March 2024.
IN JULY 2024, WE SIGNED A BUSINESS ALLIANCE AGREEMENT WITH WAAM3D, A UK-BASED 3D PRINTER MANUFACTURER, CRANFIELD UNIVERSITY, WHICH HAS WORLD-CLASS KNOWLEDGE OF WAAM TECHNOLOGY, AND AICHI SANGYO CORPORATION, WHICH WAS ONE OF THE FIRST COMPANIES IN JAPAN TO ENGAGE IN METAL 3D PRINTING. THE BUSINESS ALLIANCE WAS THE START OF THE LARGEST SCALE PRODUCTION OF PROPELLANT TANKS IN JAPAN.
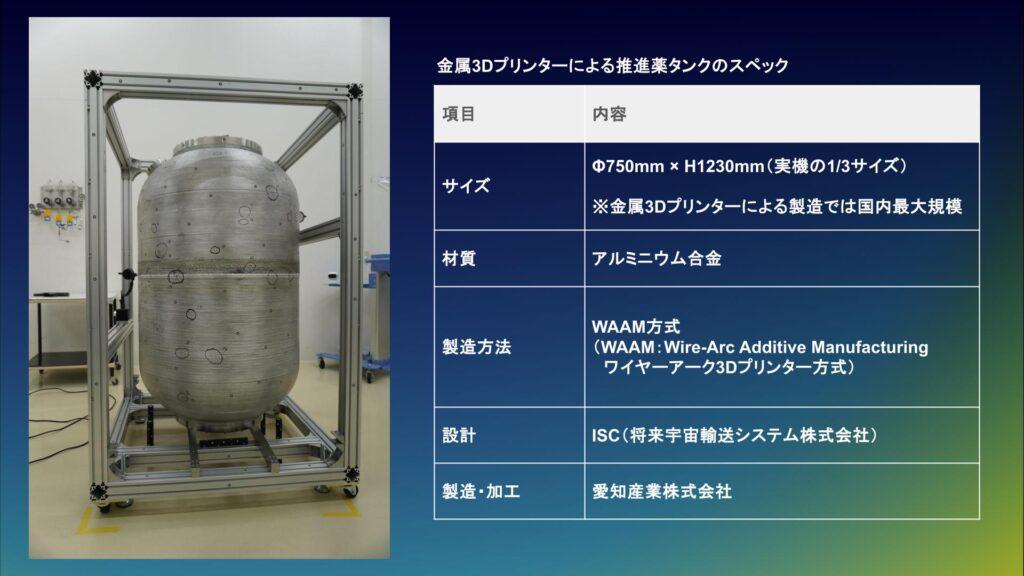
ON FEBRUARY 4 (TUE.) AND 5 (WED.), 2025, WE CONDUCTED A PRESSURE RESISTANCE TEST AND AN AIRTIGHT TEST OF THE PROPELLANT TANK MANUFACTURED BY A METAL 3D PRINTER.
Conducted pressure resistance and airtightness tests. Confirmation that target values were achieved.
In the pressure resistance test, it was confirmed that it could withstand the target pressure of 0.76 MPa.
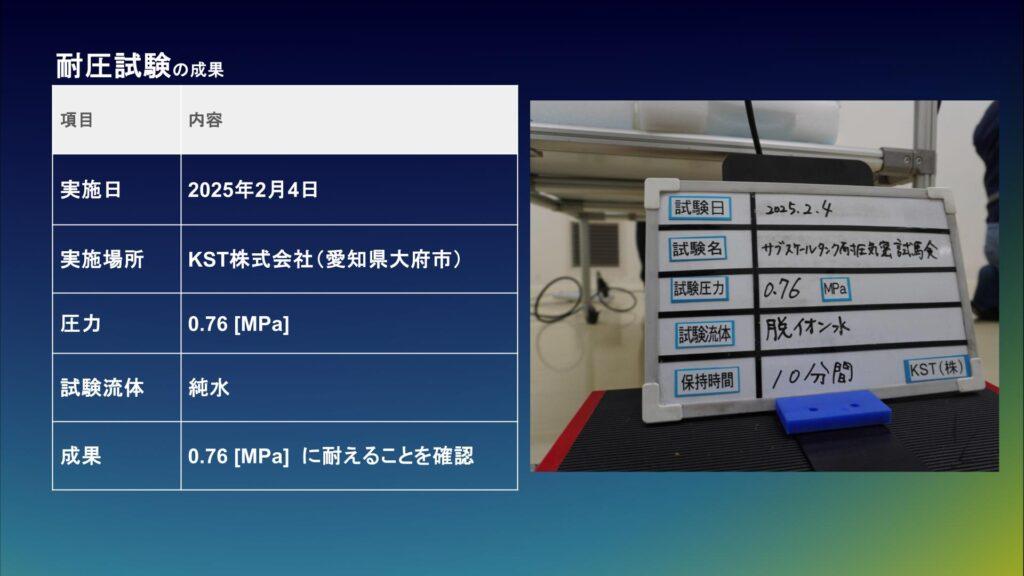
In the subsequent airtightness test, it was confirmed that there was no leakage, etc., at the target pressure of 0.69 MPa.
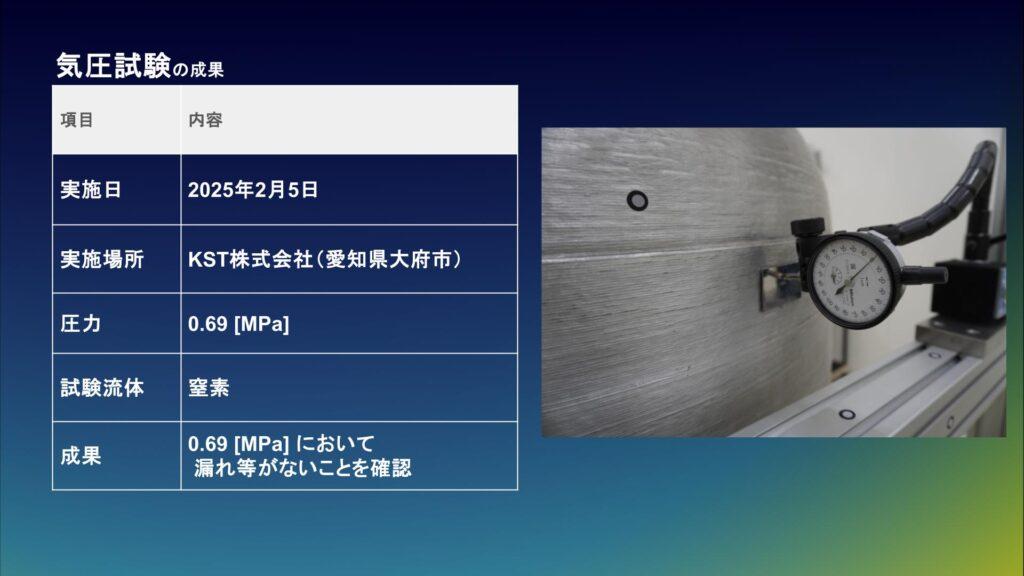
Aiming to manufacture airframe structure, etc.
BASED ON THE RESULTS OF THE PRESSURE RESISTANCE AND AIRTIGHTNESS TESTS, THE FOUR COMPANIES WILL WORK TOGETHER TO UTILIZE METAL 3D PRINTERS TO CREATE THE PROPELLANT TANK AS WELL AS THE AIRFRAME STRUCTURE TO BE USED IN THE ACTUAL ROCKET AIRFRAME.
Others Reference image
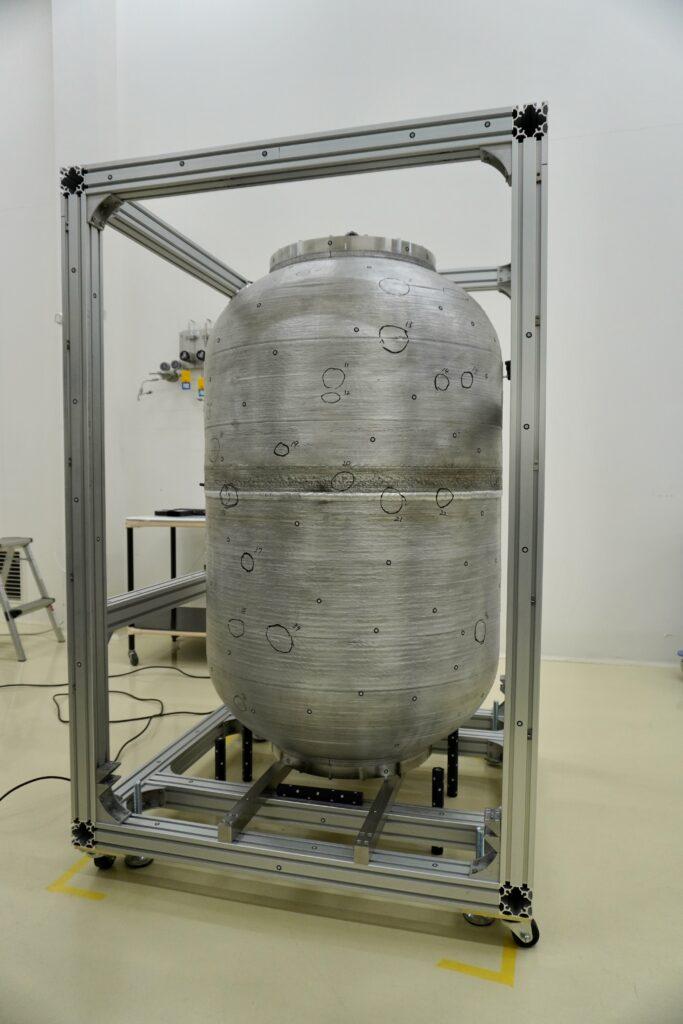
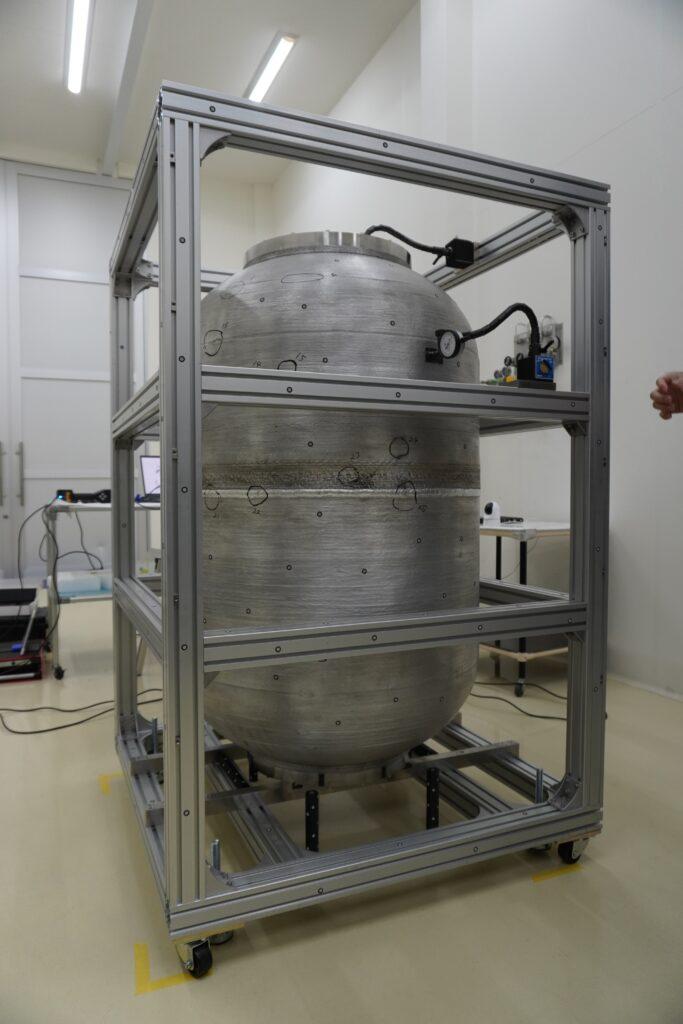
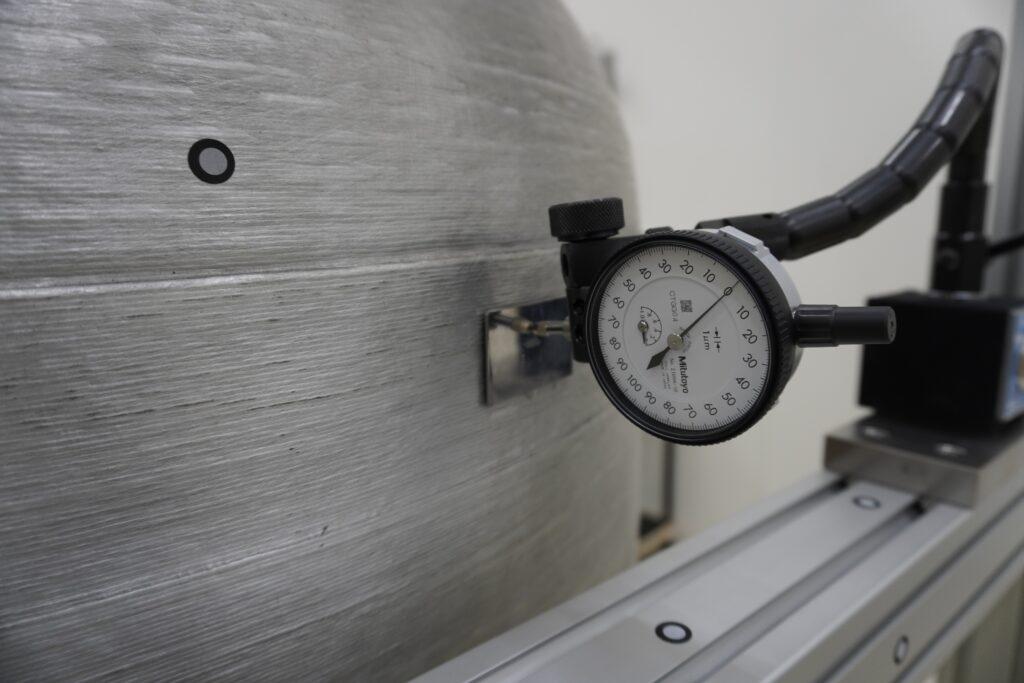
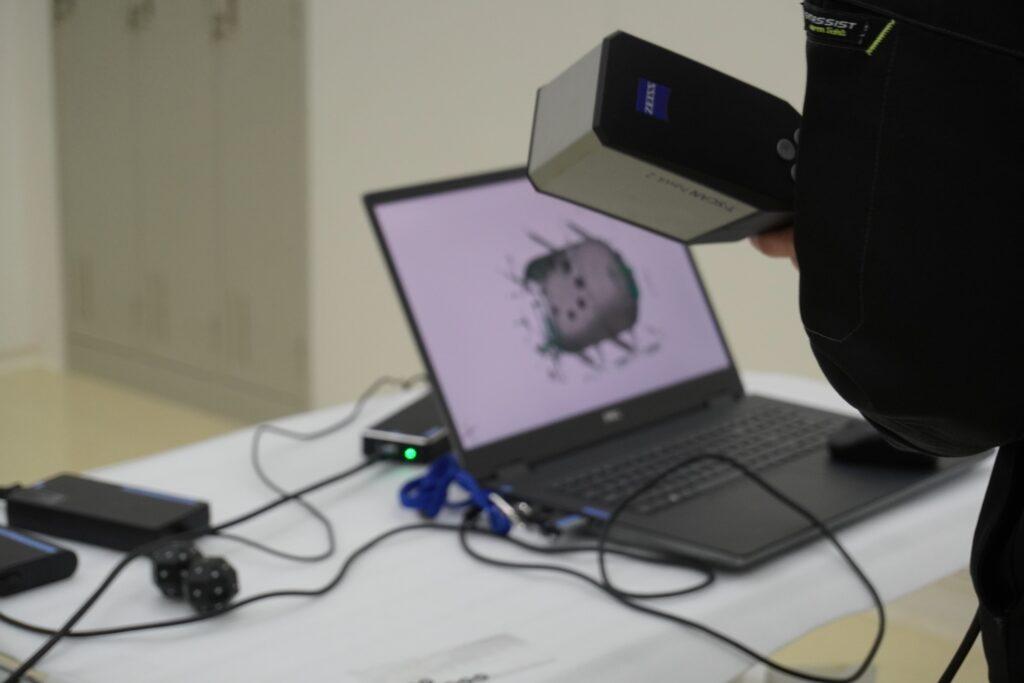
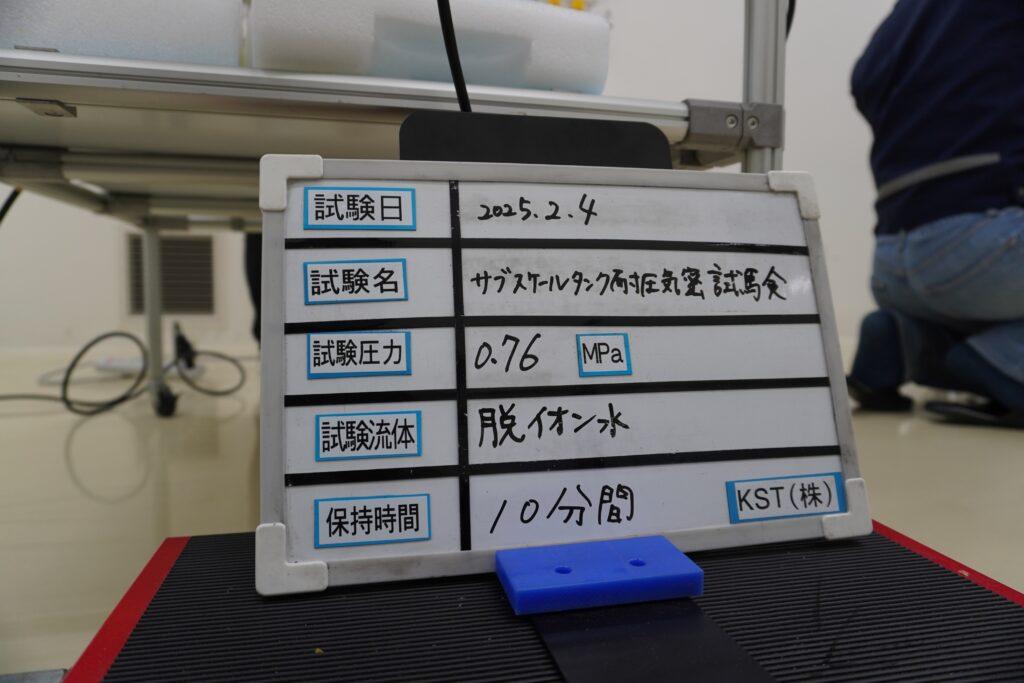
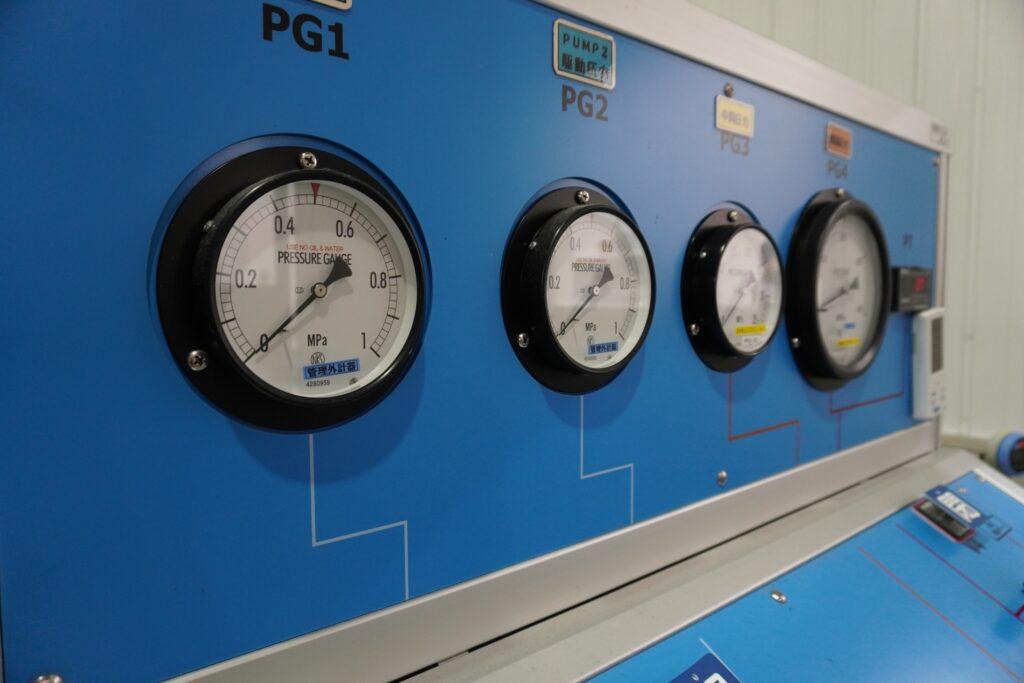
■We are actively recruiting personnel!
We want to go to space from Japan.
We take on challenges.
Aerospace technology x Knowledge of different industries x Backcast thinking
Create new industries with an eye on the future.
Let's do a job worth challenging with our life.
Click here for the employment page:
https://www.wantedly.com/companies/company_9146989
For business partnerships and other inquiries, click here
https://innovative-space-carrier.co.jp/contact/
■We are accepting "advanced applications" for space travel
Please follow this link to register.
https://forms.gle/TDc8HpdcR2zCU41t9